Parte 1: Engrenagem e peças de suspensão automotiva
1. Processo de usinagem de engrenagens
De acordo com diferentes requisitos estruturais, o principal processo tecnológico de processamento de peças de engrenagem é forjar blanks → normalização → usinagem de acabamento → modelagem de engrenagem → chanframento → fresagem → barbear → (soldagem) → tratamento térmico → retificação → corte de malha.
Os dentes geralmente não são usinados após o calor, exceto os dentes principais e secundários ou as peças que o cliente necessita para triturar os dentes.
2. Fluxo do processo do eixo
Eixo de entrada: forjamento de tarugos → normalização → usinagem de acabamento → laminação do dente → perfuração → modelagem do dente → chanframento → fresagem → raspagem → tratamento térmico → retificação → corte de malha.
Eixo de saída: forjamento de tarugos → normalização → usinagem de acabamento → retificação e fresagem → raspagem → tratamento térmico → retificação → guarnição de emparelhamento.
3. Fluxo de processo específico
(1) Forjamento de tarugos
O forjamento a quente é um processo de forjamento em branco amplamente utilizado para peças de engrenagens automotivas. No passado, os blanks de forjamento a quente e extrusão a frio eram amplamente utilizados. Nos últimos anos, a tecnologia de laminação de cunha cruzada foi amplamente promovida no processamento de eixos. Esta tecnologia é especialmente adequada para fazer blanks para eixos escalonados complexos. Não só tem alta precisão, pequenas tolerâncias de pós-processamento, mas também alta eficiência de produção.
(2) Normalizando
O objetivo deste processo é obter dureza adequada para o corte posterior da engrenagem e preparar a estrutura para o tratamento térmico final, de modo a reduzir efetivamente a deformação do tratamento térmico. A normalização geral é muito afetada por pessoal, equipamentos e ambiente, dificultando o controle da taxa de resfriamento e uniformidade da peça, resultando em grande dispersão de dureza e estrutura metalográfica irregular, o que afeta diretamente a usinagem e o tratamento térmico final.
(3) Usinagem de acabamento
Para atender aos requisitos de posicionamento do processamento de engrenagens de alta precisão, tornos CNC são usados para o acabamento de blanks de engrenagens. O furo interno e a face final de posicionamento da engrenagem são processados primeiro e, em seguida, o processamento da outra face final e o diâmetro externo são concluídos simultaneamente. Ele não apenas garante os requisitos de verticalidade do furo interno e da face final de posicionamento, mas também garante que a dispersão de tamanho da produção de blocos de dentes em grande escala seja pequena. Assim, a precisão do blank da engrenagem é melhorada e a qualidade de processamento das engrenagens subsequentes é garantida.
Existem três formas principais de posicionamento e fixação para o processamento de peças de eixo:
1. Posicionamento com o furo central da peça: No processamento do eixo, a coaxialidade de cada superfície externa e face final da peça e a verticalidade da face final em relação ao eixo de rotação são os principais itens de sua posição mútua precisão. A base do projeto dessas superfícies é geralmente Ambos são a linha central do eixo. Se forem usados dois furos centrais para posicionamento, está de acordo com o princípio da coincidência do ponto de referência.
2. O círculo externo e o furo central são usados como referência de posicionamento (um grampo e um topo): embora a precisão de centralização seja alta, a rigidez é baixa, especialmente ao processar peças mais pesadas, não é estável o suficiente e o corte quantidade não deve ser muito grande. Durante a usinagem de desbaste, para melhorar a rigidez da peça, a superfície externa do eixo e um furo central podem ser usados como referência de posicionamento para o processamento. Este método de posicionamento pode suportar um grande momento de corte e é o método de posicionamento mais comum para peças de eixo.
3. Use as duas superfícies circulares externas como referência de posicionamento: Ao usinar o furo interno do eixo oco (por exemplo: usinar o furo interno do cone Morse na máquina-ferramenta), o furo central não pode ser usado como referência de posicionamento , e as duas superfícies circulares externas do eixo podem ser usadas como referência de posicionamento. dado de posicionamento. Quando a peça de trabalho é o fuso da máquina-ferramenta, os dois munhão de suporte (referência de montagem) são frequentemente usados como referência de posicionamento, o que pode garantir a coaxialidade do furo cônico em relação ao munhão de suporte e eliminar o erro causado pelo desalinhamento dos dados.
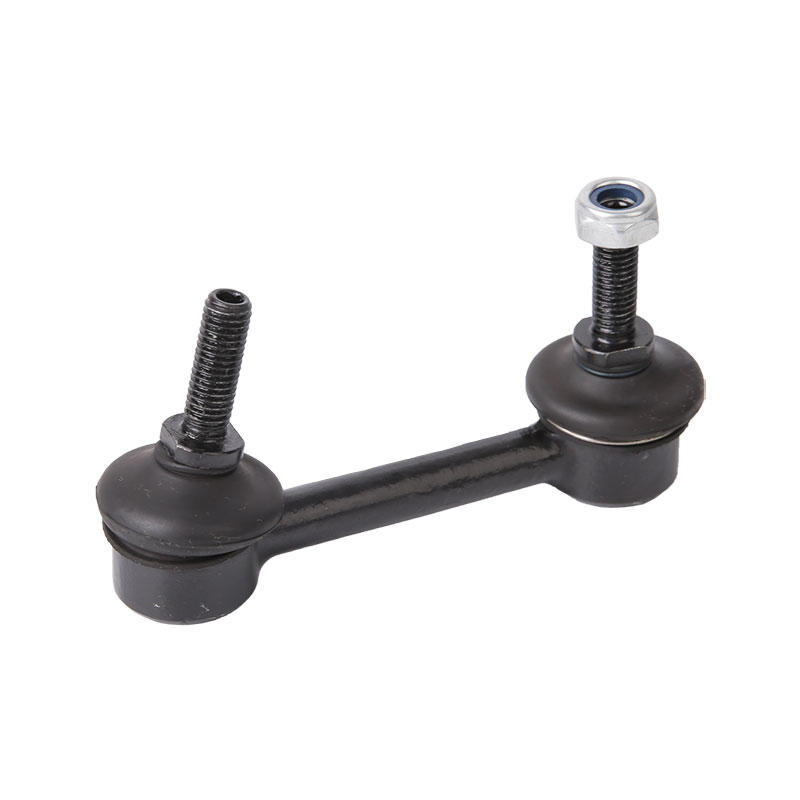
Parte II: Peças do casco
1. Fluxo do processo
O fluxo geral do processo é a fresagem da superfície da junta → usinagem de furos de processo e furos de conexão → furos de mancal de mandrilamento desbastado → furos de mancal de mandrilamento fino e furos de pino de localização → limpeza → detecção de teste de vazamento.
2. Método de controle
(1) Acessórios
O processo de usinagem da caixa de transmissão é considerado um exemplo de "Usinagem do centro de usinagem vertical. Processo 10# Usinagem do centro de usinagem vertical Processo 20# Usinagem do centro de usinagem horizontal Processo 30#", são necessários três conjuntos de acessórios do centro de usinagem para evitar peças. a deformação de fixação também deve ser considerada, como interferência da ferramenta, operação flexível, várias peças e uma braçadeira e comutação rápida.
(2) Aspecto da ferramenta
No custo de fabricação de autopeças, o custo da ferramenta representa de 3% a 5% do custo total. A ferramenta composta com estrutura modular possui características de alta precisão, porta-ferramentas reutilizáveis e pequeno estoque, sendo amplamente utilizada. Pode encurtar muito o tempo de processamento e melhorar a eficiência do trabalho. Portanto, quando os requisitos de precisão não são altos e as ferramentas padrão podem obter melhores resultados de processamento, as ferramentas padrão devem ser usadas o máximo possível para reduzir o estoque e melhorar a intercambialidade. Ao mesmo tempo, para peças produzidas em massa, o uso de ferramentas compostas não padronizadas avançadas para peças com requisitos de alta precisão pode melhorar a precisão da usinagem e a eficiência da produção.